Crafting Perfection: Exactly How to Accomplish High-Quality Light Weight Aluminum Castings Every Single Time
In the world of aluminum casting, the pursuit of excellence is a continual journey that calls for a thorough approach and a keen understanding of the details entailed. Accomplishing regular high-grade light weight aluminum spreadings demands a thorough grasp of the processes, from choosing the ideal alloy to carrying out specific mold and mildew designs and carefully regulating casting specifications. The real proficiency lies in the capability to execute these components effortlessly to produce flawless castings every time. As we check out the details of crafting perfection in light weight aluminum castings, discovering the key strategies and strategies that bring about remarkable outcomes comes to be extremely important for those striving for quality in this specific area.
Recognizing Aluminum Casting Procedures
Light weight aluminum casting procedures, vital in the manufacturing market, involve the intricate improvement of liquified light weight aluminum into solid types with a collection of meticulously regulated actions. Recognizing these procedures is paramount to attaining top quality light weight aluminum castings continually - about aluminum casting. The main approaches made use of in light weight aluminum spreading are die casting, sand casting, and investment casting
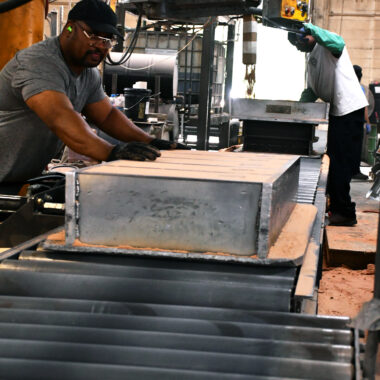
Each of these procedures has its advantages and is chosen based upon factors like complexity, quantity, and desired coating of the aluminum spreading. about aluminum casting. Comprehending the ins and outs of these methods is critical for suppliers intending to produce premium light weight aluminum castings constantly
Selecting the Right Light Weight Aluminum Alloy
Picking the suitable light weight aluminum alloy is a critical choice in the production of top notch light weight aluminum castings. When picking a light weight aluminum alloy for casting, it is important to think about the particular demands of the application to make sure optimal efficiency.
Among the most typically used aluminum alloys for casting is A356. This alloy provides exceptional castability, high stamina, and excellent corrosion resistance, making it suitable for a vast array of applications. Conversely, 6061 light weight aluminum alloy is favored for its premium weldability and great mechanical properties. For applications requiring high stamina, 7075 aluminum alloy is a preferred option because of its exceptional strength-to-weight proportion.
Along with mechanical buildings, considerations such as cost, availability, and post-casting processes should also influence the option of the appropriate light weight aluminum alloy. By carefully evaluating these factors, manufacturers can ensure the manufacturing of high-quality recommended you read aluminum spreadings that fulfill the wanted requirements.
Applying Correct Mold And Mildew Layout
Creating an effective mold layout is important for making sure the successful manufacturing of premium aluminum castings. Correct mold design plays a substantial duty in accomplishing the desired features of the end product. To implement an effective mold and mildew design, elements such as product circulation, cooling rates, and component geometry need to be meticulously thought about.
One key aspect of mold and mildew design is making certain appropriate filling and solidification of the light weight aluminum within the mold dental caries. This includes developing jogger and gating systems that help with smooth steel flow and protect against issues such as air entrapment or incomplete dental filling. Additionally, integrating cooling channels right into the mold style helps manage solidification prices and decrease the threat of porosity or shrinkage flaws.
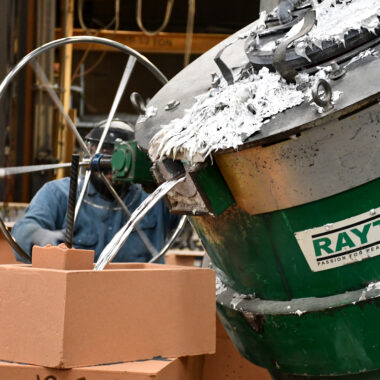
Controlling Spreading Parameters
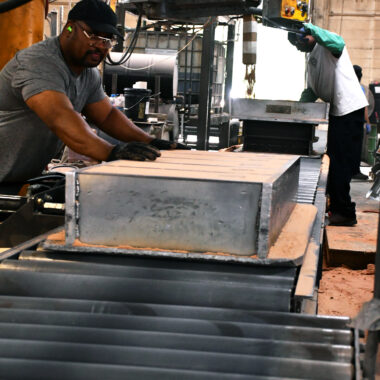
Making Sure Post-Casting Quality Checks
To maintain the excellent quality of aluminum castings, detailed post-casting quality checks are crucial. After the casting procedure is completed, it is crucial to make sure that the final items meet the preferred standards top article and specs. Among the primary high quality checks entails examining the surface area coating of the castings to determine any kind of problems such as porosity, fractures, or surface area irregularities. This visual assessment is frequently supplemented by non-destructive screening approaches like ultrasonic testing or dye penetrant examination to spot interior imperfections that might jeopardize the honesty of the casting.
Dimensional precision is an additional essential facet that must be verified during post-casting quality checks. Measurements of key dimensions and tolerances should be taken to confirm that the spreadings adapt the required specifications. Additionally, mechanical residential properties such as firmness, tensile stamina, and effect resistance may need to be evaluated through material testing to ensure that the castings have the essential toughness and durability for their intended application.
Conclusion
Finally, attaining top quality aluminum spreadings calls for a thorough understanding of the casting procedures, choosing the suitable alloy, developing mold and mildews efficiently, regulating spreading specifications meticulously, and performing post-casting high quality checks vigilantly. By following these actions, makers can regularly generate light weight aluminum castings that fulfill the greatest standards of high quality and performance.
Attaining constant high-quality light weight aluminum castings requires an extensive understanding of the processes, from picking the proper alloy to performing specific mold layouts and thoroughly controlling spreading parameters. The main methods used in light weight aluminum casting are pass away casting, sand spreading, and financial investment casting.
Financial investment casting, likewise known as precision spreading, involves developing wax patterns that are coated in ceramic to develop mold and mildews.Choosing the ideal aluminum alloy is an essential decision in the production of high-grade aluminum castings.Making certain precise control over casting criteria is essential for preserving uniformity and top quality in aluminum casting production.